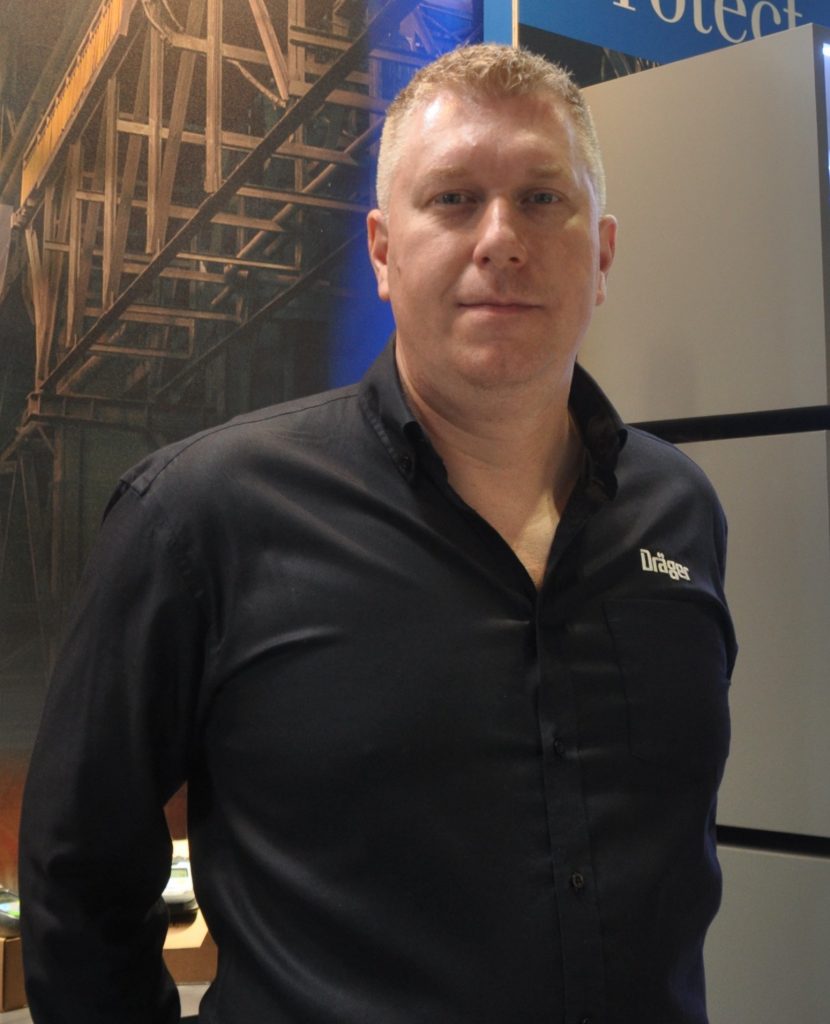
Gas detection and monitoring has long been a key part of health and safety in the water industry, and it is a topic that is rising up the agenda.
A range of issues are bringing additional focus to the subject, including those associated with increased lone working post-Covid, as well as the UK wastewater industry’s growing deployment of anaerobic digestion and biogas facilities.
With growing scrutiny by the Health and Safety Executive (HSE), it is widely expected that regulations in relation to gas safety will come underincreasing – and stricter – focus in the future.
However, whilst critical to the safety of those working in the water industry, gas safety can feel like a complex and challenging issue, not least with recent advances in connected and digital ‘Industry 4.0’ technologies
Industry 4.0
The concept of technological connectivity boosting outcomes is not a new one. The term Industry 4.0 can be traced back as far as 2011.
More than 15 years later, the ideas and technologies that were prophesised as part of the fourth industrial revolution have indeed brought far-reaching benefits to many areas of industry. From big data and cloud computing to predictive maintenance, Industry 4.0 has positively impacted many areas of the water industry. Yet safety is the one area within industry, including the water sector, where its full potential is yet to be fully adopted and embraced.
The possibilities for Industry 4.0 technologies when it comes to gas safety in the water industry are significant, and there have been some major advances in innovation within this area over recent months. From real-time monitoring of hazardous environments such as sewers, to interconnecting systems which communicate and respond to one another to safeguard personnel across a clean water site, the applications are wide-ranging. And early adopters are seeing significant benefits.
Connected gas safety in water operations
Gas hazards exist in a wide range of applications in the water industry, from treatment units, tanks, service reservoirs, chemical handling and storage areas, to pumping stations wells, sumps, overflows, boreholes, sewers and manholes. The most frequently occurring hazards are flammable gases such as methane and fuel vapours, toxic gases such as hydrogen sulphide, and also oxygen displacement. But there are also risks of oxygen enrichment where oxygen injection is used for wastewater treatment, and chlorine, sulphur dioxide and ozone for clean water treatment.
Gas detection is therefore a critical and a life-saving measure to ensure the safety of engineers and other personnel, but also to ensure the safety of plant equipment.
As part of a robust gas safety solution, portable gas monitoring devices would be issued to all field engineers – potentially several thousand individual devices. Using new innovation in this space, a connected smart safety system can now be created to link all of these devices.
This offers a number of key benefits, including live monitoring; whereby key information is displayed in real time via an online user interface. This interface is available to anyone who has the appropriate permissions, meaning that workers on site, or managers in a central location, can pinpoint the position of their colleagues and the status of their gas safety at any given moment. If an alarm is activated by any individual device, colleagues and managers would be immediately alerted to the risk, and receive the key information displayed on the management dashboard. Furthermore, emergency services can be granted access to the data which allows them to manage an emergency situation, if needed, and the data is also logged for later analysis.
This means that hazards can be identified more quickly; countermeasures can be initiated faster, and correlations and anomalies can be analysed more easily to identify root causes. This is important in improving outcomes, not only in post-event analysis, but in real-time through live monitoring.
Another key benefit of this type of digitisation is that it offers opportunities for more efficient asset management, simplifying a range of processes that were previously more complex, and centralising management, whilst decentralising execution.
This makes device management and compliance far more straightforward, as data in relation to operational status, testing and calibration results can be collected and accessed from anywhere, with the ability for analysis to be performed directly. Device updates can also be distributed centrally with ease, notifications can be sent to users, and a complete documentation history for each gas detection device is automatically stored on the connected system.
Increased transparency, easier management and reduced potential for human error are key outcomes of such a smart system, leading to significantly improved safety to life, and also cost savings at the same time.
Driving digital innovation
In this example, as with so many others, Covid has served as a catalyst to drive digital innovation, with changes to working styles prompting an urgent need for remotely accessible real-time safety data. At the same time, pressures on budgets across the water sector mean that any new safety solutions or technology must be able to prove itself financially.
Savvy companies – including some of the leading names in the water industry – are increasingly recognising, however, that the cheapest up-front cost doesn’t always mean the highest quality product, or indeed the most efficient total lifetime cost. This is particularly true when you consider that digital systems allow for easier bolt-on of new or additional elements to an overall system.
Well-designed and forward-thinking connected and digital safety can deliver on all fronts with the right planning and consideration of what is needed both now and in the future. But it is vital that good training, and a thorough understanding of such technologies is well-embedded as part of any new roll-out. Without this, there is a real risk that the full benefits may not be realised.
With demand growing throughout the industry to generate better safety insight and information to better inform safety policies and approaches, there is a huge demand for safety data. And whilst this may feel challenging, advances in safety technologies are making this increasingly possible, and straightforward.
As connected and digital safety is starting to become increasingly better understood and harnessed in the water industry, and alongside the range of operational benefits, this new technology herald’s new potential to safeguard those exposed to gas safety risks in the sector.