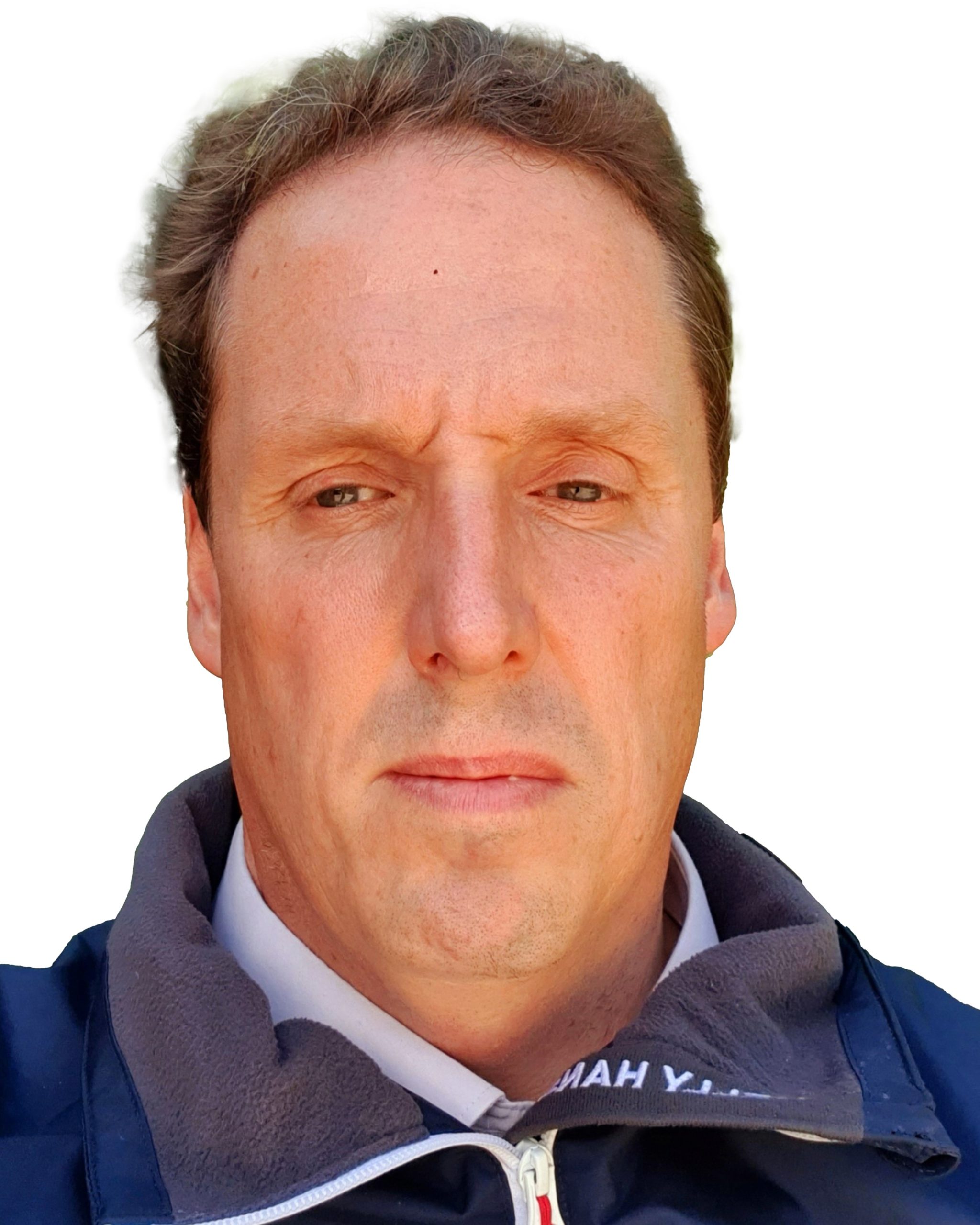
In his regular column, Oliver Grievson, Associate Director AtkinsRéalis and Royal Academy of Engineering Visiting Professor at the University of Exeter, explores the rise of the digital twin.
Although the concept of a digital twin was first applied to the manufacturing industry in 2002 the actual term was first coined in 2010 by NASA. But it was 2014 before it started to be mentioned in the water industry when it was adopted by the German Water Partnership.
The originally definition of the term “Digital Twin” was overly complex and talked about the merging of cyber and physical systems to create a co-joined cyber-physical system. This definition has changed significantly over time and is much clearer on what a Digital Twin actually is:
A Digital Twin is a virtual representation of a physical system that contains data from various sources, such as sensors, forecasts, and model data.
However even this is up for debate as the reality is we have to break down the use of cases of what Digital Twins actually are – especially within the water industry. When we get industry specific we can understand not only what the technology is and what it promises, but how we can apply it to the water industry. Digital Twin technology can be split into at least three different areas.
Construction Digital Twin –There is a comparison here to an advanced form of 3-D autocad, where we can produce a virtual copy of an asset, be it a collection network or a wastewater treatment works. This is not only to understand how it will work on-site but also how the construction process can progress, and it provides an opportunity to test the functionality of the system before construction has begun. This can have the principles of BIM applied to it and we have a virtual copy of a works before it begins. As construction progresses this becomes a powerful asset management tool.
Asset Digital Twin – A number of companies are producing micro-Digital Twins at Asset Level. This is especially useful for asset reliability engineering of high value assets such as blowers, large pumps and critical process units. This can be applied to high criticality assets where down-time is going to significantly adversely affect the running of processes and close monitoring of the performance is necessary.
Operational Digital Twin – On a more holistic based systematic scale we can have Digital Twins throughout both the water and wastewater systems. One of the first and most advanced Digtial Twins was applied as a hydraulic version of the water distribution network, and this provides a very powerful tactical tool for use in the control room but over time there have been case studies developed of the wastewater collection network and wastewater treatment plants.
As the concept of the Digital Twin develops there will undoubtedly be more categories that emerge. What is clear from the experience of those who have developed Digital Twins within the global water industry is that when you apply them there does have to be a specific use-case in mind, and the Twin that is developed will have a natural bias to that use case.
Over time as different uses are applied then the bias of the original Digital Twin emerges. This takes the development of the models that represent the physical system and the instrumentation layer which informs the current state of play and gives a level of situational awareness. There is an iterative process to go through to develop the models (be they mechanistic or data-based) and developing the data sources.
What is clear however is that Digital Twin technologies have a huge potential in the modern water industry to address some the largest of problems we face. The current collaborative project using Digital Twins to drive towards net zero is groundbreaking as an example of where the technology can be applied, but there are also so many different applications such as in the wastewater network and in river systems to not just show where issues lie, but also hopefully reveal what we can do to improve our aquatic environment.