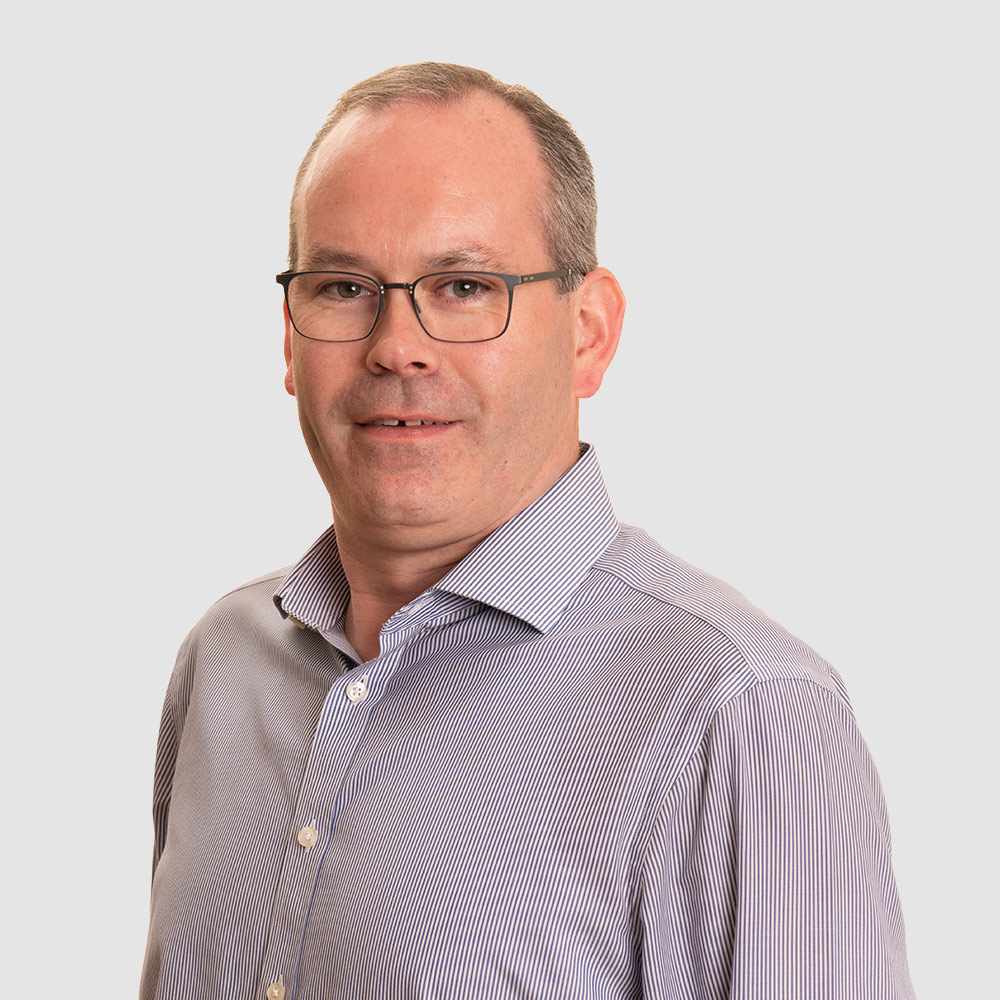
Across the pump industry, businesses working in a range of sectors are increasingly realising the importance of proactively monitoring pump health, helping them to spot any potential issues in advance.
Common problems like blockage and bearing failures can lead to unexpected breakdowns of the production line, meaning businesses miss deadlines, face a backlog of orders, encounter inevitable customer dissatisfaction and loss of revenue.
The food and beverage industry, which processes thick, glutinous materials or debris-laden waste water on a daily basis is particularly vulnerable here, estimated to waste around £180 billion a year through lost productivity, with total downtime accounting for 5 to 20 percent of their working time.
As well as the financial consequences, there can be more serious repercussions of poor pump management, if, for example, pumps within a washdown system have aged, become inefficient, and are in need of replacing. This situation could lead to the failure of a washdown system and infringe on strict hygiene compliance.
What is clear is that, without regular monitoring, minor issues can escalate into major problems. Yet while routine observation is the norm in many industries, they do not detect the issues at the early stages.
Being proactive
Businesses are turning to technology as part of the solution, showing a growing appetite for smart pumps, which feature remote monitoring. Indeed, a recent report stated that the sale of smart pumps is expected to gain traction of 7.8 percent CAGR (compound annual growth rate) between 2023 and 2033.
This trend isn’t surprising, given the benefits of remote monitoring. The ability to track the status of pumps anywhere in the world with an internet connection, allows businesses to identify issues before they worsen and turn into risks.
Should there be an alarm or fault, key players in the business can receive a text message or email altering them, with common triggers including a fluctuation in water flow rate – indicating a blockage – loss of power, or a tripped pump.
Timely action can then be taken. If, for example, a business was to receive a severe message, letting them know their pump station was about to reach full level, a member of the team could check the control panel – assessing whether the pumps have tripped, whether the power is on, or if the pumps are still set in automatic mode.
If there were other signs of fault in the panel, they could also reset the system accordingly and – if the alarm still sounds – an engineer can be quickly called out to assist with the solution, preventing a more catastrophic and costly outcome such as flooding or loss of water supply.
The more advanced monitoring systems offer dashboards displaying useful data and trendlines. Advanced algorithms allow the operator and maintenance teams to determine issues weeks before they cause a visible issue. This maximises the up-time of the systems.
Empowering customers
Remote monitoring also caters to those that are simply after the peace of mind that their operation is running smoothly, with the choice to opt in for ‘all clear’ messages.
We’re seeing a growing number of businesses looking to improve their understanding of the overall health of their pump systems, while reducing the need for costly engineer callouts.
Remote monitoring takes away the need for regular on-site checks, which is only becoming more important against the backdrop of the engineering skills gap.
Nevertheless, for the best results, it’s important to balance innovation in technology with existing talent. For one, it’s skilled pump engineers who choose the right pump systems for customers, configured and operated to achieve efficient water distribution and maintain consistent pressure – minimising downtime.
It’s an exciting time for the industry, with discussion already arising about how developments in Internet of Things (IoT) technologies could advance monitoring capabilities even further. IoT-enabled sensors could collect additional valuable data such as water quality monitoring based on parameters such as pH, turbidity, and chlorine levels.
To read other insights from the Dura Pump team, visit https://www.durapump.co.uk/