Nearly 7 in 10 organisations operating in the utility sector admit that they are unlikely to comply with on-the-spot Health & Safety Executive (HSE) inspection due to a lack of data proving that their fixed and moveable assets are managed and maintained to the required regulatory standards.
Nearly one fifth (18%) of utility companies have received enforcement action in the past due to assets not meeting HSE compliance standards, with 10% receiving an HSE fine.
The new research on 500 people working in the utility and renewables sector, in roles responsible for asset management and maintenance, formed part of a larger study commissioned by enterprise asset management (EAM) solutions specialist, BPD Zenith. The full study involved 2,000 respondents operating in the telecoms and broadband, as well as the defence, transport, pharmaceutical, and healthcare sectors.
The findings revealed that over half (51%) of these utility organisations’ data isn’t detailed, nor updated or recorded accurately enough to comply with the Health and Safety at Work Act 1974 or other HSE regulations that apply to their sectors.
Latest HSE figures for 2022/2023 show that there were 60,645 employee non-fatal injuries reported by employers during this period and 135 deaths as a result of work-related accidents. The Health and Safety at Work Act 1974 legally and duty bounds companies to ensure a safe working environment for employees and third parties, including the general public, who may be affected by an organisation’s activities. The HSE compliance standards work alongside the Health and Safety Act, designed to protect people and the environment. Penalties for failure to comply can include fines, orders for operations to cease, and imprisonment if the misconduct is found to be serious enough.
88% of respondents in the sector did acknowledge that improvements to their asset management systems and processes are required to drive up the quality, completeness, and consistency of their data. Asset management systems are operational processes and tools that help manage the performance and maintenance of fixed or moveable assets. These assets include everything from production and manufacturing machinery to equipment found in buildings such as HVAC systems, elevators, and security doors, and any vehicles used in day-to-day operations.
Nearly a third (32%) also confirmed they still use outdated paper-based methods in part or in full to record, update, and store maintenance data, with over half using Excel spreadsheets, rather than leveraging digital asset management solutions.
Amongst the priority improvements to their asset management strategies, 69% recognised the need for enhanced data quality, 56% highlighted improved analytics, and 49% identified a need for better systems integration with their existing EAM solutions.
Findings also identified a greater demand from utility companies for improved field-based, mobile data capturing and utilisation solutions. 41% of respondents said recording data in the field, not being able to record data at the point of work, a lack of intuitive forms, and not having technical data and maintenance manuals at the point of use, were the biggest challenges to keeping asset management and maintenance data updated. Access to real-time inventory levels (20%) and struggling to plan, schedule, and dispatch work to multiple crafts and contractors (10%) were amongst the other challenges organisations faced.
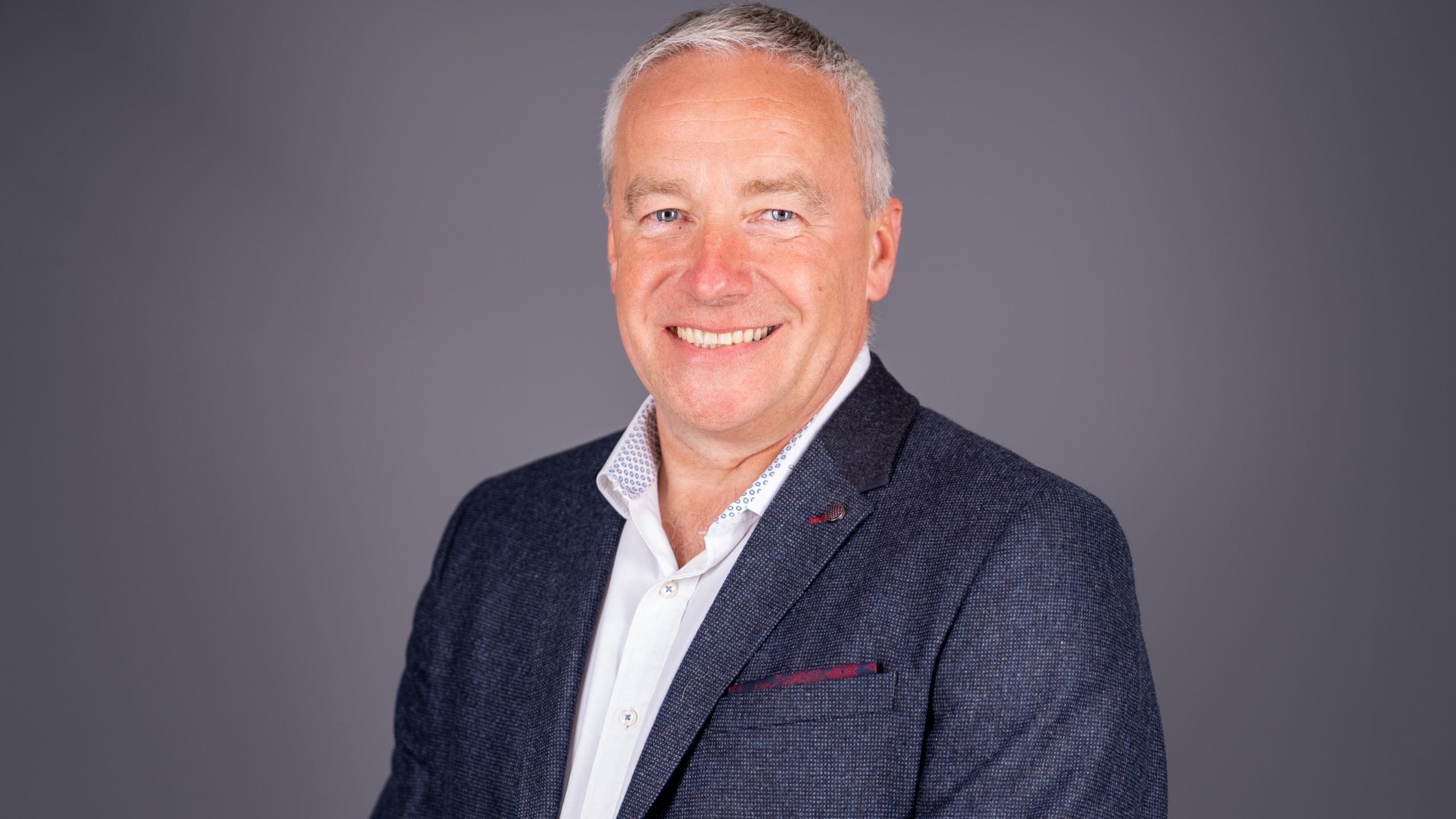
Roger Walker, Group Head of Innovation at BPD Zenith said:
“The results from this survey have been surprising in part. However, what they do identify is that 80% of these companies probably aren’t where they need to be in their asset management digital transformation journey. What they need to identify though is why. Do they have the right asset management strategy, processes and tools in place? If not, is this due to a lack of resources, either through investment in the right equipment, or software, or people, or it may be a case that data collection and analytics are not sufficiently high on their list of priorities.”
Walker continued:
“HSE inspections are essential for ensuring organisations of all shapes and sizes are adopting best practices which align to the legal standards expected on health, safety and an organisation’s environmental impact in their industries. These checks can also help pinpoint where processes may be weaker and help implement measures aimed at strengthening these areas. The penalties for non-compliance can be hugely detrimental to businesses, not just financially but reputationally too.
“We work with organisations across an extensive spectrum of UK industries including the utility and renewables sector, ranging from oil and gas, transport and logistics, and manufacturing to defence and security, life sciences and facilities management. Over recent years we have seen a growing demand for mobile solutions to support asset management amongst those organisations with large, complex and field-based estates. As well as a growing need for solutions to capture data, there is also an increasing demand for tools that support the teams maintaining these assets, whether that’s in the form of planning and scheduling tools for work order management, or intuitive solutions while they are on the job.”