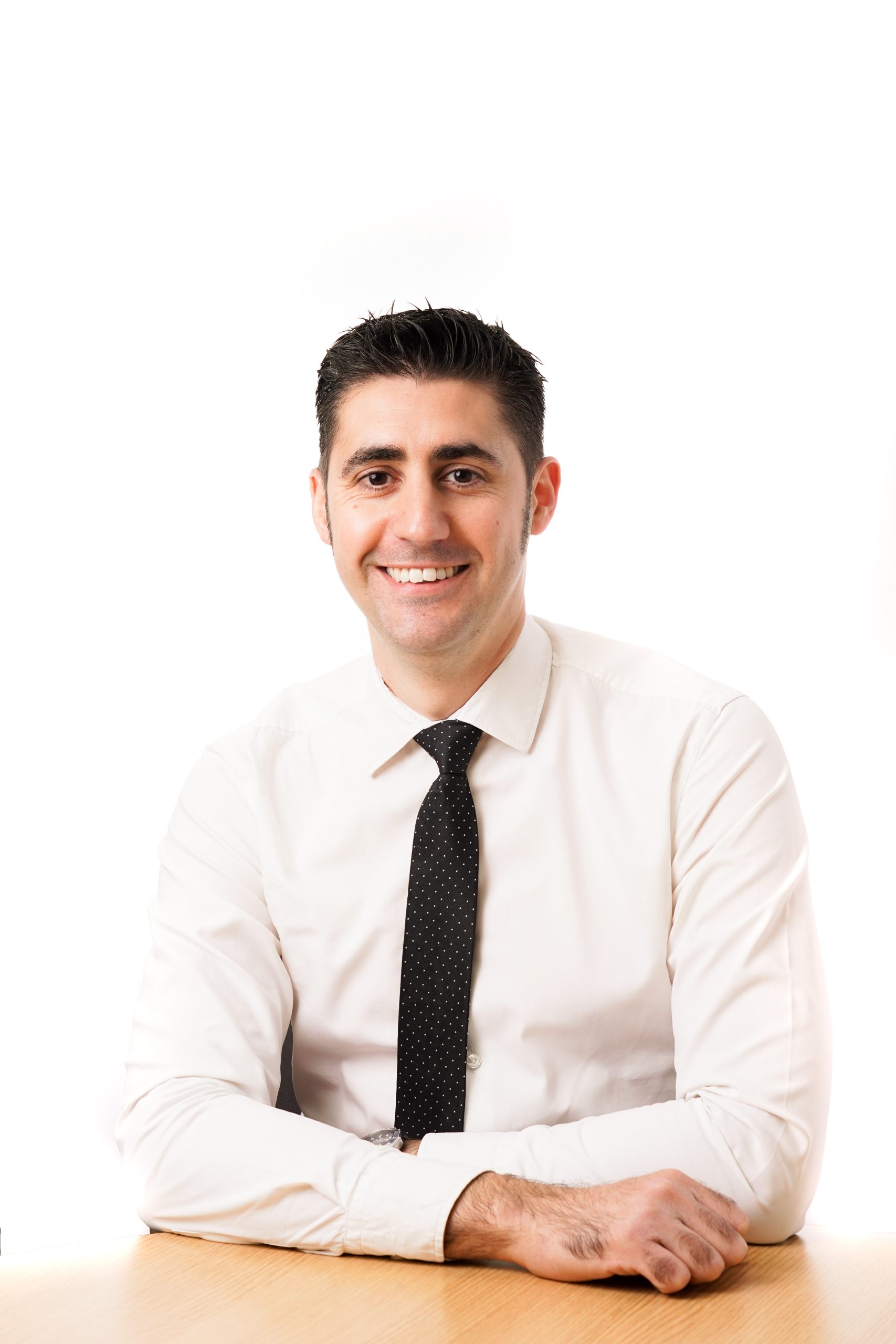
Pablo Martinez-Moore, Commercial & Marketing Director at North Ridge Pumps, has been involved in the pump industry for over 10 years, and has become a specialist in a range of pumping applications. Here, he examines the role of the filter press and considers which pumps are best suited for this essential process.
So, what is a filter press?
The first filter presses came into operation in Britain in the 1850’s and were used to separate seed oils. But it took another 100 years for the technology to fully develop and become a viable and cost-effective choice for a variety of industries and applications.
A filter press is a machine which works to separate solids suspended within a liquid known as a slurry. A filter press turns the slurry into water and dry filter cake.
They operate by receiving the slurry from a filter press feed pump which compresses the mixture. It separates out the variable quantities of solid-laden slurry from the water carrying it.
Filter presses and the pumps supplying them can bring big benefits to a company’s business operations:
- Removing water from slurries and sludges to cut wastewater treatment costs
- Reducing transportation and disposal costs
- Maximising plant effectiveness
- Enabling water to be reused to maximise process efficiency
How is a filter press used?
When fed by a special filter press feed pump, a filter press can be used for:
- Polishing
This removes impurities from liquids such as small clumps of sediment, water and microbes. This is often carried out with fuel.
- Fixed volume or batch
The filter press can hold a large quantity of solids, so it can be stopped and started to remove the solid waste which has been separated. This is called cake, sludge or filter cake.
- Variable volume
These units have a diaphragm or membrane plate which separates the cake more effectively than other methods. They can produce dry content of between 30% and 80% and reduce filtration time by up to 50%.
The pumps used to supply filter presses are usually positive displacement pumps as these can handle the increasing back-pressure as the filter press becomes filled with material. Filter press pumps can be designed with automatic start and stop between batches, and also to allow the filter press to be cleaned when required.
How do they work?
As the slurry is pumped into the filter press, two chambers are filled with the material. As the chambers fill, compressed air is shifted from one chamber to the other by a linked shaft that enables the chambers to move simultaneously. This back-and-forth movement forces liquid out of one chamber and into the discharge piping. At the same time, the other chamber is being filled with liquid.
When the chambers reach capacity, the liquid is filtered out by the compressed air, leaving behind solid slurry, sludge or filter cake ready to be disposed of.
Perhaps the biggest advantage of this process is that instead of having to get rid of massive amounts of wet slurry, the operator is left with water and smalls amount of filter cake. This brings down disposal costs considerably.
Therefore, a key component of the whole process is the filter press feed pump which sends the solid-laden fluid to the filter press.
Pumps to consider
Air Operated Double Diaphragm (AODD) – driven by air and has two separate diaphragms which work individually to separate the water and particles. These fill with fluid before being discharged through an outlet manifold.
High pressure AODD pump – these special high-pressure air-driven filter press pumps models work in just the same way as standard AODD pumps. The big difference is that the high pressure design has a built-in internal pressure amplifier with external piping. These enable the units to deliver pressures of up to 16 bar which is essential for many filter-press applications.
If you have a dewatering application needing the transfer of fluids, solids or viscous liquids, and aren’t sure which pump to specify, visit the North Ridge Pumps website.