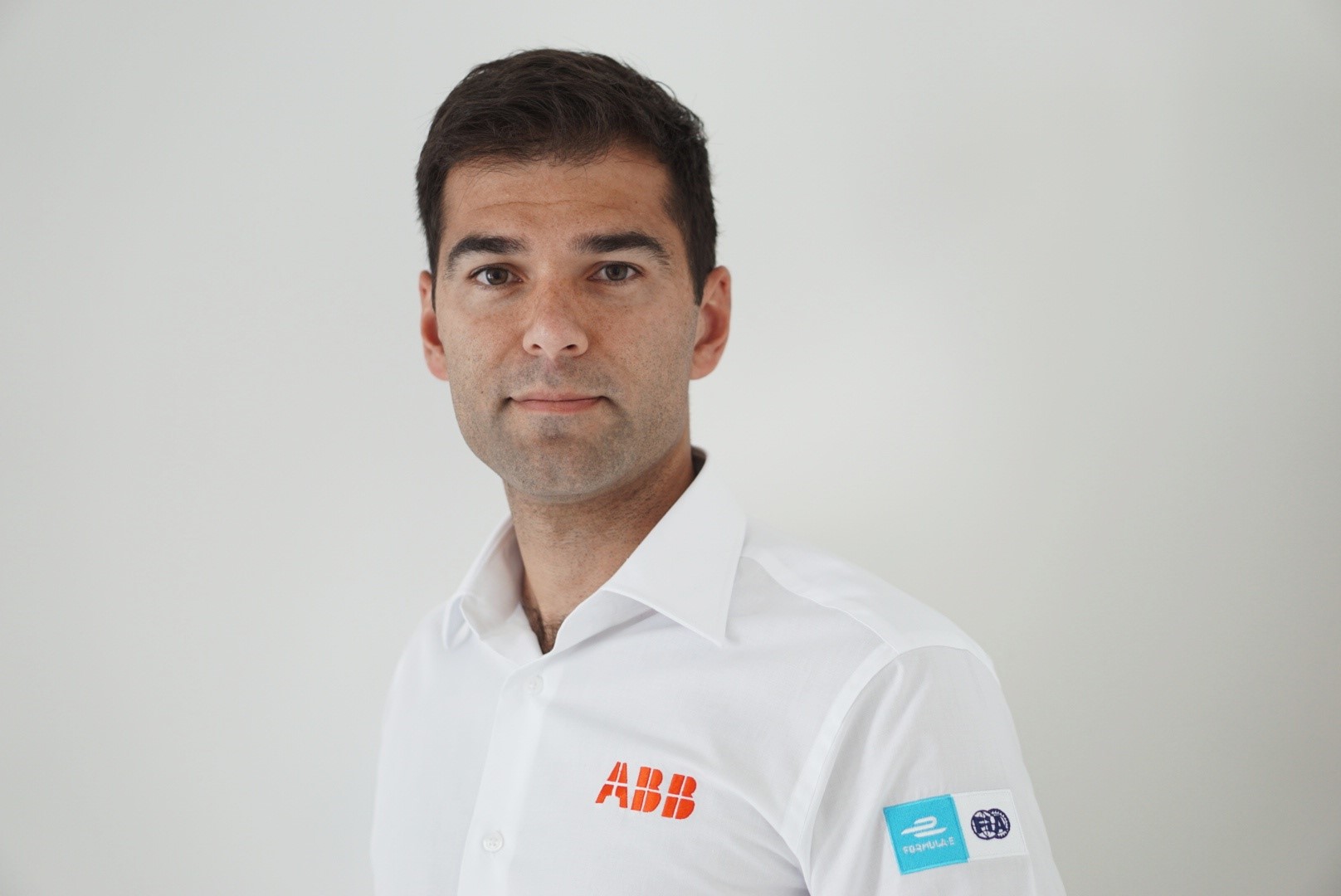
Efficiency isn’t just about having the most advanced energy-saving equipment. Significant savings can be achieved simply by using existing equipment more intelligently, as ABB’s Clayton Mead, UK Water Industry Manager, explains.
There are many thousands of pumps in operation across the UK water industry. Many of these pumps will be controlled by a variable speed drive (VSD). Simply using a drive at less than 50 Hz will reduce the motor’s energy consumption, sometimes by vast amounts. However, you can also do more.
A drive can also be used to make changes to the motor’s control philosophy, which governs how it actually operates. These changes can be big, but they can also be very subtle. Indeed, within the context of often finely-tuned water processes, making lots of subtle changes can rapidly add up to a big difference in overall system efficiency.
Pumping slower for longer
Pumping slower for longer is generally more energy efficient than pumping intensively in short bursts. Level control is a drive feature that allows a water tank or reservoir to be filled, or a wet well to be emptied at a matched rate from incoming or outgoing flow. Traditionally this would be achieved using a PLC with instrumentation to detect when levels rise or fall to predetermined points, along with float switches or other mechanical components. Level control ensures that the pumps within a configuration are operating at the best speed to balance energy efficiency against the required filling and/or emptying rate. For wet wells, this can also help to avoid caking and sedimentation.
Level control isn’t particularly radical in itself, and it’s a function that drives have offered for many years. However, when you use it to change how a pump actually operates, there are big savings available. Consider a 100,000 litre tank. If we were to pump at 1,000 litres per hour then it would take 100 hours to empty. A 100 kW pump running for 100 hours will use 10,000 kWh of energy, which equates to £2,000 in energy costs at 20 pence per kWh. If you were to instead use a drive to run the motor at 80% of the speed, this will provide a pumping rate of 800 litres per hour, and require 125 hours to empty the tank. This reduces the total energy required to 6,250 kWh, which equates to £1,250 in energy costs – a 35% saving.
Two pumps are better than one
Since centrifugal pumps are variable torque applications, running two pumps at 60 percent speed can end up costing less to move the same volume of water compared to running one pump at 100 percent speed. Intelligent Pump Control (IPC) is a drive feature which permits the easy integration and operation of multi-pump systems, which typically consist of several pumps, each connected to a separate drive. This arrangement enables a high degree of flexibility in load sharing, balancing the run time between the pumps and keeping each pump in the configuration running optimally.
Multi-pump systems achieve a high level of redundancy, whereby if one pump fails or requires maintenance, then others can utilise spare capacity to pick up the slack. It can also help to reduce the strain on any one pump, potentially reducing maintenance requirements while prolonging its lifetime.
Reducing blockages
Blockages in wastewater treatment are a problem that often faces water utilities. It most often occurs when debris gets trapped around the pump impeller, causing it to seize up. The pump must then be extracted from the wet well, cleaned and then reinstalled. As well as being expensive to fix and requiring specialist lifting equipment, this also creates downtime and can also have implications for health and safety. It can also incur a carbon cost in mobilising the heavy equipment required, as well as the crews to operate it.
Some drives can deal with this problem through an anti-jam or anti-ragging function. This commands the pump to go through a series of forward and reverse rotations to shake off any build-up rags or other debris on the impeller – the pump can then continue with normal operation. As well as preventing potential blockages before they can happen, this improves pumping efficiency, and decreases the need for manual inspections and cleaning.
In summary
When you make many small changes across the tens of thousands of motors used across the industry, this can add up to substantial energy savings. A conservative estimate suggests that improvements in operating efficiency could cumulatively help the water and wastewater sector to save up to £60 million per year in energy costs.
If you’d like to find out more about how to make your processes more energy efficient without the hassle, search for “ABB Water Challenge”.