A 3D concrete printed structure has been installed at Yorkshire Water’s second largest wastewater treatment works, following a collaboration looking into how more sustainable materials can be used in the construction process.
A 3D concrete printed structure has been installed at Yorkshire Water’s second largest wastewater treatment works, following a collaboration looking into how more sustainable materials can be used in the construction process.
Finnish technology company Hyperion Robotics, working in collaboration with building materials company Tarmac and engineering company Mott MacDonald Bentley, created four 3D printed versions of a drawpit, which will be used at Esholt wastewater treatment works, based on the outskirts of Bradford.
A traditional drawpit would have been a 5.2m square structure used to allow electronic cabling to change direction, and usually made from concrete.
This 3D printed drawpit is a 2.2m diameter circular structure made from reinforced concrete, composed of two faces as formwork and sandwiching a traditional reinforced cast concrete core, weighing five tonnes, and almost half the size of a traditional drawpit.
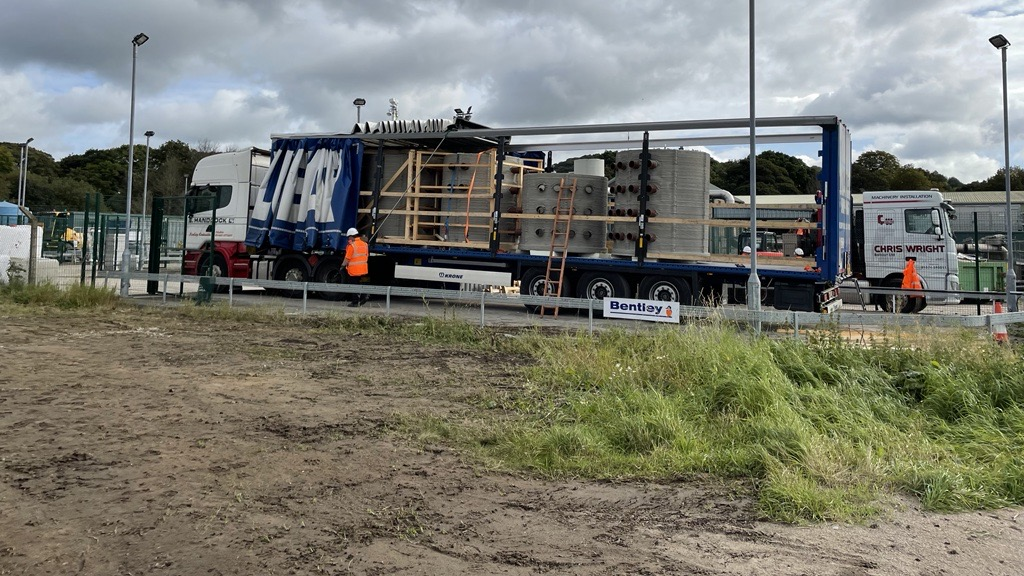
Each drawpit took around two hours to print, with pipes and reinforcement installed. After curing, they were then cast with self-compacting concrete, before being delivered to Esholt from Finland.
The drawpits were successfully installed at Esholt’s newly refurbished pumping station and have been positioned ready to accept the electronic cabling that helps with the water filtration on site.
Yorkshire Water’s senior project manager Joe Fisher said:
“It’s a fantastic piece of innovation and it’s been great for Yorkshire Water to get involved.
“It’s important for Yorkshire Water to do all it can to reduce our embodied carbon by looking at low-carbon solutions so we can reach our target of becoming net-zero. Forming partnerships and investing in products such as this, helps us achieve our aim of becoming more sustainable. This initiative has allowed us to achieve a 40 per cent reduction in embodied carbon for this element of work, which is a great result.
“If this drawpit is successful, there are several other sites that are undergoing investment and upgrades that will benefit from this type of construction.
“I’d like to thank Hyperion, Tarmac and MMB for collaborating on this project, and we look forward to seeing where this takes us next.”