RS, a global provider of industrial products and services including maintenance and safety solutions, has unveiled findings from a report based on survey responses of participants in the utilities, telecoms and oil, gas and energy sectors, which have highlighted some of the key challenges facing maintenance engineers in those sectors.
RS partnered with the Institution of Mechanical Engineers (IMechE) to survey its members. While the overall survey included almost 700 maintenance engineers in the UK and Ireland, this Industry in Motion report focuses on the responses of 125 participants from the utilities, telecoms and oil, gas and energy sectors, working in job roles like engineering and maintenance management. The top three challenges respondents cited as expecting to affect them over the next 12 months were attracting talent (42 per cent), supply chain disruption (39 per cent) and declining department resource (34 per cent).
The report also delves into a key issue: drivers of unscheduled downtime and its cost to a business. Ageing assets and mechanical failures are the biggest drivers of unscheduled downtime. The report revealed nearly 20 hours are spent each week on unscheduled maintenance by engineers in these sectors, compared with less than 17 hours spent each week on scheduled maintenance. This is at an average hourly downtime cost of £6,804.10.
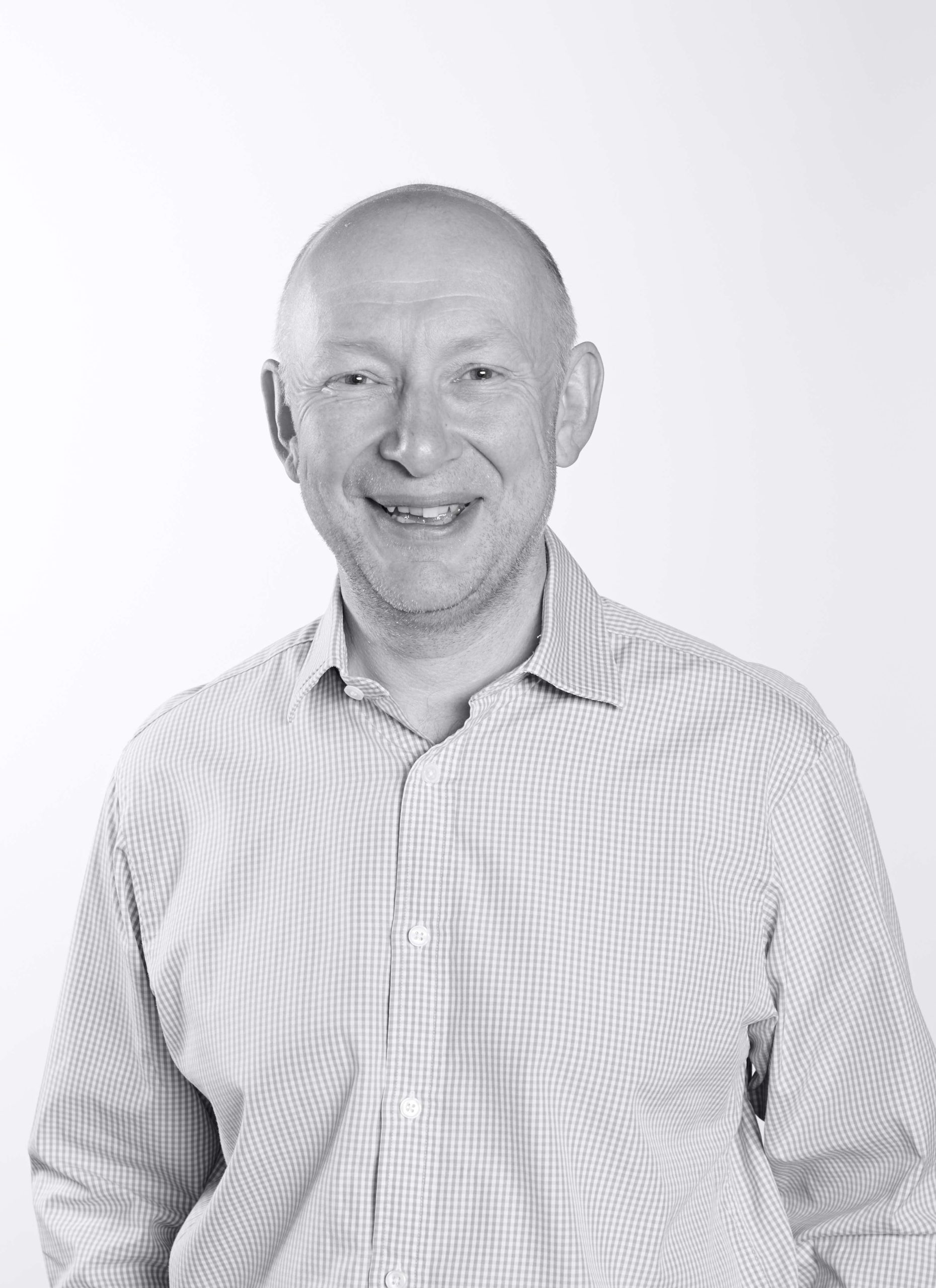
Chris Cruise, industry sector manager for utilities, power and communications at RS, said: “Across all the industries represented in the survey, the biggest driver of unscheduled downtime is ageing assets. However, a greater percentage of those in the utilities, telecoms and oil, gas and energy sectors put this in the number one spot: 39 per cent as opposed to 28 per cent overall.
“This is unsurprising, given the amount of 19th and 20th-century infrastructure underpinning these industries and the difficulties of replacing assets at scale. And although they’re always investing, these organisations can’t simply go and replace the entire water and waste system, or the whole electricity network,” he added.
When it comes to using condition monitoring to help with predictive and preventative maintenance, the three top techniques used within the utilities, telecoms and oil, gas and energy sectors are vibration, current monitoring and oil analysis. These were also the top three techniques in the overall survey, but use of them is higher in these industries at 54 per cent compared to 44 per cent for vibration, 50 per cent versus 43 per cent for current monitoring and 46 per cent compared to 38 per cent for oil analysis.
It’s not surprising, given the challenges facing the economy and businesses of all sizes, the Industry in Motion report found that many of the targets set for maintenance engineers in these sectors are around financial performance. In the overall survey, the top three key performance indicators (KPIs) used to measure the achievements of maintenance engineers were maintenance cost and replacement asset value, budget adherence and maintenance backlog, all reported by a third or more of respondents.
And while 28 per cent of respondents overall were being measured against failure analysis, this rose to 46 per cent for respondents in the utilities, telecoms and oil, gas and energy sectors – making it the most common maintenance KPI for engineers in these industries.
Cruise believes this is because water, waste, communications and power are such critical national services.
“If there’s any failure, it puts your lights out, it turns off your taps, it stops your internet, so there are consequential losses,” he said.
With attracting talent being cited in the top three challenges, respondents to the survey spoke of having to outsource activities. Six in 10 made this decision because too many specialised skills were required, while 42 per cent cited lack of skills among staff. And 45 per cent of maintenance engineers said they took the step simply because they had reduced headcount. Just over a quarter said the decision was prompted by budget issues.
RS believes this could become a growing trend, as 21 per cent of respondents in these sectors said they envisioned a need to outsource in the next 12 months, compared to 10 per cent overall, with perceived benefits including flexibility, topping the list at 43 per cent.
Cruise said: “These industries have lots of ageing assets. They need a wider range of options available to source the parts and make sure that they’re genuine and fit for purpose. The flexibility of outsourcing helps with this. Plus if, for whatever reason, the solutions’ provider cannot get the genuine part, they have the expertise to find a suitable alternative that will work and tick all those other boxes around governance as well.”
While less than a fifth of respondents from these sectors rated their organisation’s maintenance maturity level as high, they are more likely than average to be using predictive maintenance (50 per cent compared to 38 per cent overall).
With the rise of the Industrial Internet of Things (IIoT) connected devices, the survey confirms technology is making a difference in these sectors: more than nine out of 10 firms said they were using Computerised Maintenance Management Systems (CMMS) or Enterprise Asset Management (EAM) to monitor and manage maintenance. RS thinks this is because the geography of infrastructure encourages an embrace of digital technologies, as many of these organisations have a strong foundation of earlier technologies, like telemetry. However, only 30 per cent of respondents claimed their company is planning a digital transformation of maintenance assets and facilities, so there is still a way to go.
Cruise concluded: “The thing that comes across clearly from our survey is that maintenance engineers are practical people. They’re problem-solvers with an eye on technology to help them keep ageing assets in use, even in the face of cost pressures and supply disruption. They will engage suppliers to help them meet new challenges and, above all, they will continue to tackle downtime and improve process efficiency wherever they can.”
The Institution of Mechanical Engineers (IMechE), is a global organisation with around 115,000 members and holds the mission to improve the world through engineering.
The RS and IMechE ‘Industry In Motion’ 2023 Maintenance Engineering Report for the utilities, telecoms, gas, oil and energy sector can be downloaded in full here.