The upgrade of chemical dosing equipment at a wastewater treatment plant in Germany is delivering high performance sludge dewatering through more reliable polymer dosing.
Safe and reliable chemical dosing helps wastewater treatment plant (WwTP) operators meet the required environmental standards at the facilities they manage every day of the year.
A WwTP in Heide, a small town in Schleswig-Holstein, Germany, has upgraded the polymer dosing pumps in its sludge conditioning process with specialist peristaltic pumps to reduce the maintenance interventions and polymer leaks it experienced previously with screw pumps.
In Germany, strict regulations for harmful chemicals, pharmaceutical residues, and microplastics mean the opportunities for reusing wastewater sludge as agricultural fertiliser are increasingly limited and sending it to a landfill is usually not permitted. This means thermal recycling is becoming more accepted as an effective route to sludge disposal, but the required dewatering and polymer dosing during the sludge conditioning process can add significant costs.
Identifying cost-efficiencies in the dewatering process can mean significant savings for wastewater treatment plant operations and a significant reduction in the amount of sludge produced. In the case of Heide WwTP, deploying a Qdos chemical metering pump from Watson-Marlow Fluid Technology Solutions (WMFTS) to replace a screw pump has made a big difference.
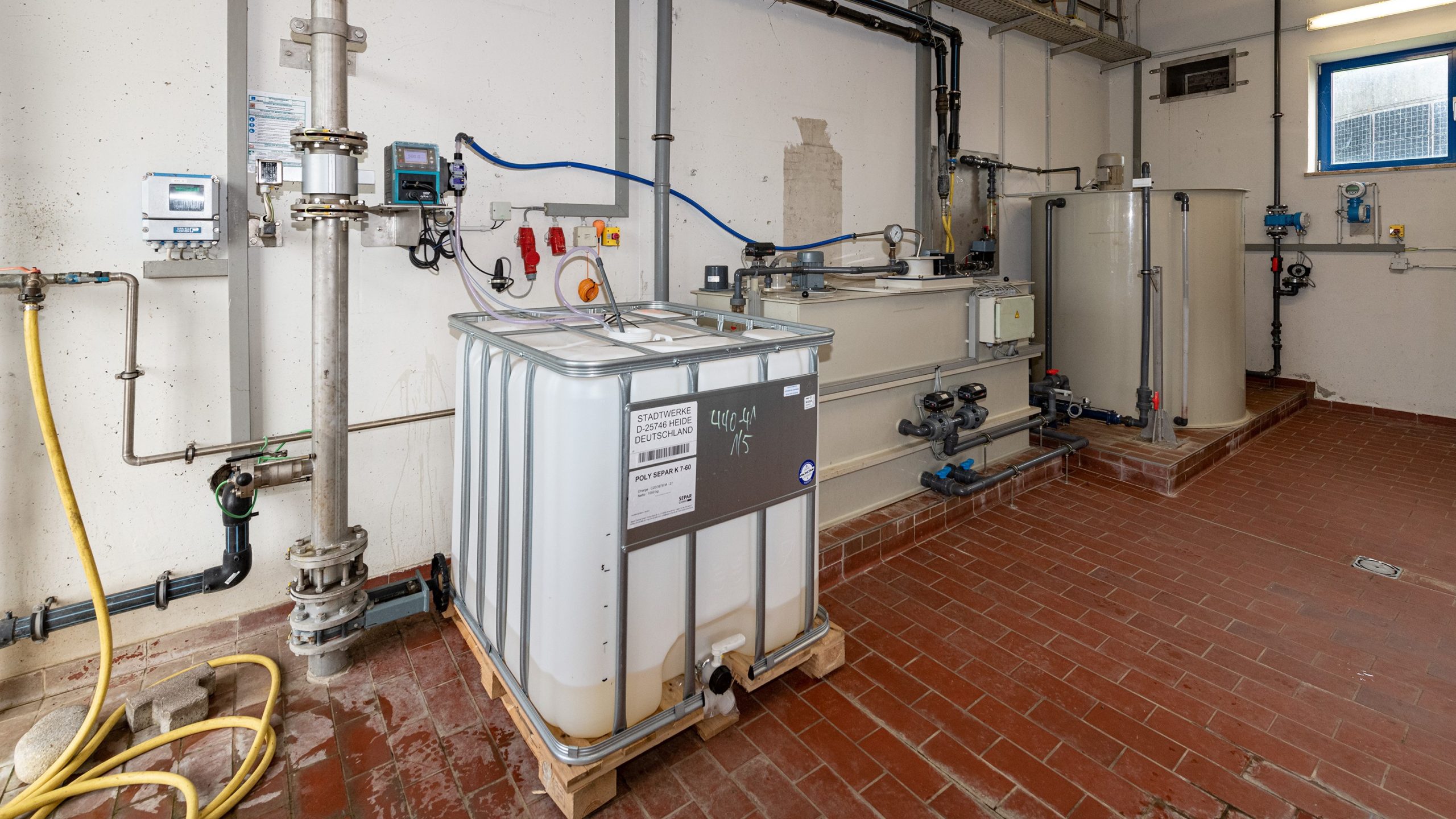
High accuracy
The WwTP installed a Qdos 60 PU peristaltic pump, which is specially designed to dose hard-to-process polymers, and other hydrocarbons, with high accuracy.
In most cases, polymers are used as a flocculant in the sludge dewatering process, binding together micro or nano sized particulates to form larger ‘flakes’. This improves the effectiveness of the solid-liquid separation system later in the sludge conditioning process. Selecting the correct polymer and ensuring it is used efficiently achieves the best possible sludge dewatering outcomes.
Qdos 60 PU peristaltic pumps easily achieve this high standard of polymer dosing and are crucial to this process. The low-maintenance pumps are easy, safe, and quick to service, offering substantial benefits in terms of time-saving and onsite health and safety, producing a streamlined and reliable process.
Sludge reduction
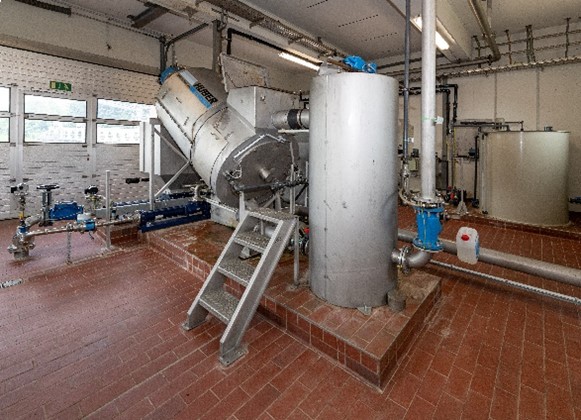
Sludge conditioning happens daily at Heide WwTP, which has the capacity to serve a population of 40,000.
“We’ve modernised our sludge conditioning process considerably in recent years,” said Peter Dohrn, wastewater treatment & technical department manager at Abwasserzweckverband Region Heide (AZV Heide).
“The sludge is thickened by adding an oil-based polymer flocculating agent and then fed through a screw press, which removes the water. This thickened sludge is then transported into the digestion tank, where it stays for up to 25 days before being dewatered again. After this, it is transported to the storage site before being collected for use in agriculture.”
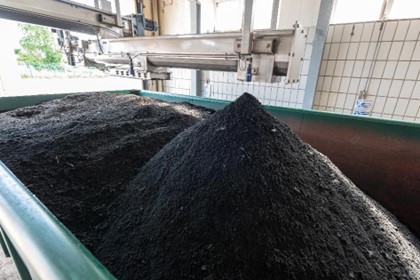
Sludge is processed at a rate of 7m3/hour, and conditioning reduces the volume by 80%, increasing the dry residue from 0.71% at the beginning of the process to 4.83% at the end. Each polymer dose takes around five minutes and occurs six times a day.
The process needs a pump which can deliver this repeatability and is robust against the polymer’s viscosity and resistance to pumping. Therefore, dosing pump reliability is critical to ensuring the sludge is thickened in a cost-effective and time efficient way.
Maintenance and operation
Previously, progressive cavity pumps were used to dose polymers at Heide WwTP, but they were difficult to operate and required frequent servicing. Since progressive cavity pumps cannot run dry, suction from the intermediate bulk container (IBC) had to take place via the outlet fitting on the bottom of the IBC.
This made changing the IBC time-consuming and often caused minor leaks. The most serious problem though was the lack of leak detection during operation. This meant that if a tube failed, the entire polymer contents in the container could leak out leading to a loss of expensive polymer and additional maintenance, as “a slippery mess on the floor would require intensive cleaning,” said Dohrn.
Additionally, the amount of time and effort involved in servicing the screw pumps, due to the different parts coming into contact with the polymer, was a growing problem.
“Every servicing run involved several hours of work (with the screw pumps),” Dohrn explained. “Also, the extremely heavy progressive cavity pump was hard to move around, and its working principle meant it couldn’t achieve the dosing accuracy of other pumps due to its design.”
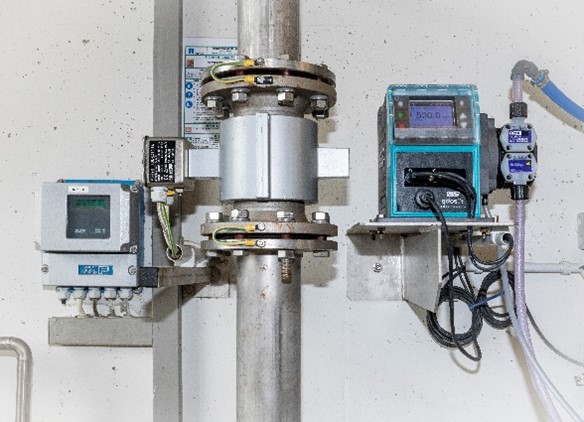
Pumphead replacement
The Qdos 60 PU peristaltic pump provided an effective solution, with no need for diaphragms, valves, or seals that could be clogged by the polymer.
It also has a highly innovative design principle as the only part on the pump that ever requires replacement is the patented ReNu 60 PU pumphead. It is simply removed as a single unit and a new one clicked into place.
As the pumphead is fully sealed, there is no risk of the polymer leaking or the operator coming into contact with chemicals during replacement.
Leak detection
The pumphead has an integrated leak detector which automatically stops the pump and displays an error message if the tube ruptures. This also eliminates the risk of contamination caused by leaking polymer.
“In comparison to our previous pump, the Qdos has a much higher level of safe chemical handling and operational safety,” said Dohrn.
The intermittent dosing process is regulated from an external control system and has an accuracy of ±1 per cent. “Thanks to its highly effective suction capability, the self-priming Qdos pump can extract polymer from the IBC from above by means of a suction tube,” reported Dohrn.
“The pump handles the suction height of just under a metre with ease. The pump can also empty the polymer almost completely, reducing the risk of leakage during changeover.”
Operators at Heide wastewater treatment plant are also impressed with the durability of the new Qdos 60 PU.
“The first pumphead ran smoothly for a year before we had to replace it, purely as a preventive measure, and the second one has been working without any trouble,” said Dohrn.
Versatile in application
“The Qdos 60 PU pumphead has been specially developed to dispense the hard-to-handle polymers involved in sludge dewatering and has recently been added to the Qdos series,” explained Adeel Hassan, product manager at the Watson-Marlow Fluid Technology Solutions.
“As the model has a pump tube made of polyurethane, it is ideally suited to dosing liquid acrylamide-based polymers or aliphatic crude-oil-based hydrocarbons.
“These versatile pumps can be used for dosing liquids at up to 120 l/hr and up to 7 bars in various applications, across a range of sectors. They are available in different sizes and control options, depending on requirements.”