Variable speed drives (VSDs) have long been established as an effective tool to save energy on motor-driven processes. In recent years, the modern VSD has developed some new tricks, many of which are functions designed specifically for pumps in water and wastewater applications, as Martin Richardson, Water Framework Manager, ABB, explains.
At a basic level, a variable speed drive is a device that controls the speed of a motor. Industrial motors with no form of control will constantly run at full speed by default, yet very few applications require this. As such, having the ability to vary the speed of the motor in accordance with actual demand can save vast amounts of energy, in some applications upwards of 50 percent.
Drive technology has come a long way in recent decades. As well as delivering substantial energy savings for applications across water and wastewater facilities, the modern drive is now packed with additional features and functions that can help to improve the resilience, safety and effectiveness of pump processes.
On-board condition monitoring
For instance, using condition monitoring is the future of maintenance strategies, yet drives have already been capable of it for some time. As well as controlling a pump motor, it is also constantly receiving feedback as to how that motor is performing. Modern drives can also provide highly sophisticated monitoring of the condition of the drive itself, as well as other powertrain devices.
Variable Speed Drives contain Condition Monitoring Curves which can, for example, compare the expected torque on the motor shaft with high- and low-level limits over a range of speeds. This ensures the VSD can indicate when the load on the motor is operating in an unexpected zone and can flag this up to a PLC or control system, prompting further investigation of the mechanical equipment. All this is done without the aid of a sensor, using the VSD and a curve which is set up during commissioning.
Anti-cavitation software is another advantage found in some drives. This sensorlessalgorithm monitors the behaviour of the motor shaft to detect patterns consistent with cavitation. When detected, the drive will automatically reduce the speed of the motor to prevent cavitation from occurring, significantly prolonging the lifetime of pumping equipment.
Executive control functions
Running two pumps at 60 percent speed can end up using less energy to move the same volume of water compared to running one pump at 100 percent speed. Intelligent Pump Control (IPC) permits the easy integration and operation of multi-pump systems, which typically consist of several pumps, each connected to a separate drive. This arrangement enables a high degree of flexibility in load sharing, balancing the run time between the pumps and keeping each pump in the configuration running optimally.
Multi-pump systems achieve a high level of redundancy, whereby if one pump fails or requires maintenance, then others can utilise spare capacity to pick up the slack. In this sense, the drive is taking on responsibilities traditionally associated with a PLC, and is able to provide sophisticated level or flow control logic, potentially across multiple pumps simultaneously, without the need for an external controller.
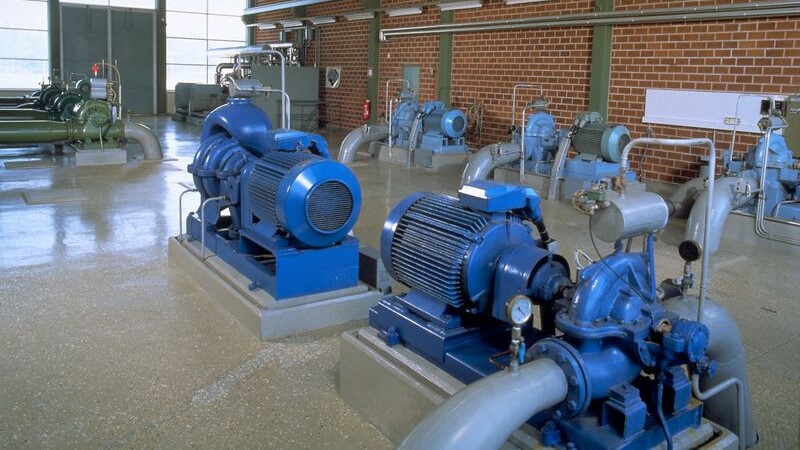
Pump cleaning
Blockages in wastewater treatment are a well-known problem. The typical way of dealing with this is to pull up the pump from the wet well, clean the pump and then reinstall it. This requires regular inspections, which creates downtime and can cause risks to health and safety.
ABB drives’ pump cleaning (anti-jam or anti-ragging) function instead uses a programmable sequence of forward and reverse rotations of the pump to shake off and remove any build-up of rags or other debris on the impeller, before continuing with normal operation. As well as preventing potential blockages before they can happen, this improves pumping efficiency, and decreases the need for manual inspections and cleaning.
ABB is inviting UK water companies to challenge us to find the untapped opportunities for energy efficiency across their facilities and operations. Changing the speed of many pumping processes by as little as 1% can improve efficiency with no negative impact, and cumulatively can help the sector to save up to £60 million per year in reduced energy costs. To find out more, search: ABB 1% Challenge