Derby Sewage Treatment Works is a large plant treating wastewater for a population of 440,000, processing an average of 1000L and maximum 2300L of wastewater per second. It is located in an industrial area in the vicinity of Spondon to the East of Derby.
The original works were built in the early 1900s and major improvements were made to the plant in the 1950s, then 1970s, before further upgrades taking place from 2000 on.
The estimated life expectancy for blowers is approximately 20 years and by 2020 the old units had reached the end of their expected life. At this time, Severn Trent decided to assess the existing blower performance to decide whether it was feasible to replace the life expired blowers with more efficient units. At that point, 2 of the originally installed 8 blowers had catastrophically failed and the site had no spare blower capacity.
David Wood – Senior Energy Project Manager at Severn Trent commissioned Air Technology Ltd to compare the performance of the existing blowers with newer, more modern machines. A selection of suitable blowers from a variety of manufactures were compared, and on this occasion, Sulzer’s HST blowers were selected as the best option. 6 Sulzer HST 20 turbocompressors were installed on the site replacing the 8 old units.
“Sulzer air blowers were the best fit for the load and air demand of the site” – says David.
When the installation project commenced, a 3rd blower failed and could have resulted in a need for hired blowers to support maximum demand, had the new blower install not been planned.
The need for blowers
In Derby, the sewers bring in the flow from the local catchment. All the flow is pumped to inlet works where large mechanical screens take out any large debris. The flow then gravitates to primary settlement tanks where any solid material settles to the bottom and sludge is drawn off, thickened, digested and the bacteria release methane. The works then use it as renewable fuel via CHP engines or used in boilers to maintain the temperature of the digesters.
The liquid that comes off the primary tanks is high in ammonia but most of the solids should have been taken out at that point by settlement process. The flow then comes to activated sludge plant (ASP) where the ammonia is taken out. There are a couple of processes where the ammonia is converted by biological processes where the bacteria make these transitions.
The first section of the ASP process is anoxic (air free). Its purpose it to starve the bugs of oxygen to allow biological processes to take place and part of the treatment is completed.
The secondary part of the process is the aerated section – bugs are fed with air and fuel (ammonia and other biological and chemical the load within the water). Sulzer air blowers play a vital role in this process – creating pressurized air to the aeration system to support the process of the ASP.
Combating the challenges with an eye for aesthetics
Commenced in November 2020 with delivery of the HSTs to the site, the project saw completion in April 2021. The installation of the blowers at Derby sewage works required the old 8 blowers to be removed through square holes in the basement roof. The 6 new Sulzer blowers were dropped down to their dedicated space through those openings and installed in the blower house. Connecting pipework was delivered and installed, replacing heavy, steel and aged pipes with thin wall stainless ones.
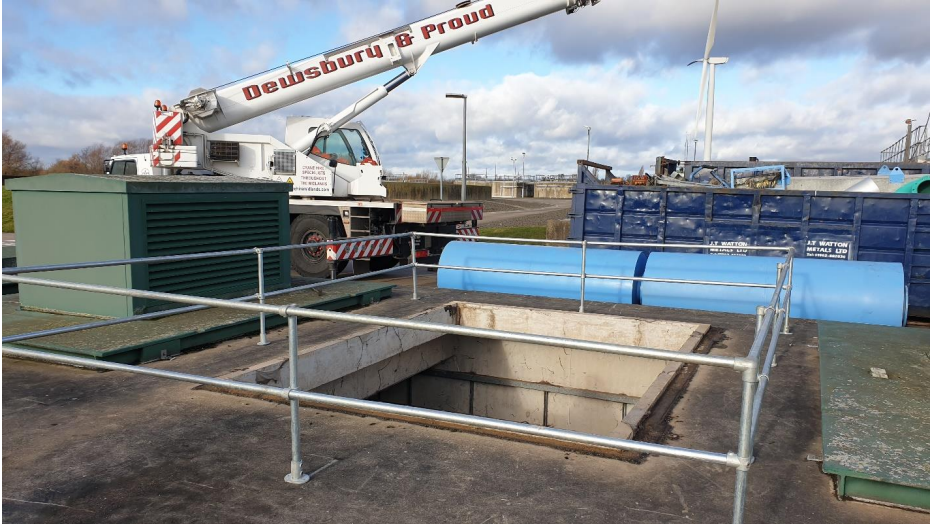
The challenge was huge due to the timing. 2020 brought restrictive pandemic conditions and a new way of working – social distancing, staggered breaks and, daily temperature checks. Sulzer being one of three contractors had to strictly follow one rule – each had a separate area they were working in at a time.
For Severn Trent there was no question of downtime. The works had to remain operational throughout the project and staff had to have access to air blowers to control the process. The switch from old control system to the new took around 2 weeks with the commissioning of a critical number of blowers to allow efficient running of the plant. This was followed by commissioning the full automation of the process. The project saw an aesthetic appeal to the design adding metal plinths to keep the Sulzer blowers in line and at same level, minimising intrusive design of pipework, pipe and cable supports.
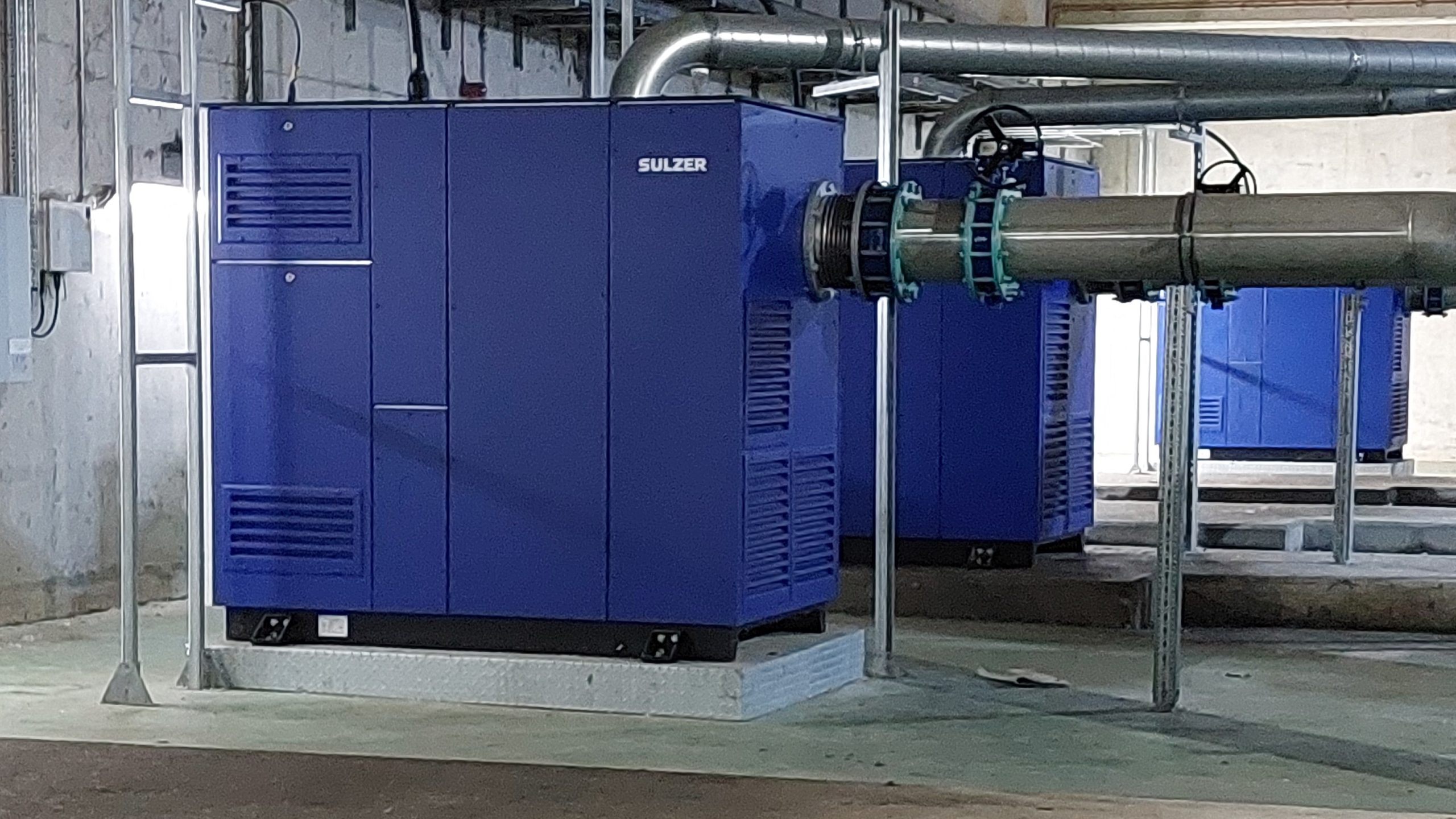
Efficiency spread over time
Having completed the installation, the new Sulzer blowers were run initially on 18th of December 2020, with full transition to the new blower on the 14th of January 2021. Since moving into automatic control, they have operated at an average 259.97kW. This would suggest an annual usage of 2.28GWh and an estimated annual saving of 1.2Gwh per year, equating to 34% blower power reduction.
Sulzer turbocompressors are optimised by MCU – Master Control Unit which calculates best efficiency for the blowers on the curve. They operate at 7,000 m3/h each at 590 mBar and at 20,000 rpm with no vibrations.
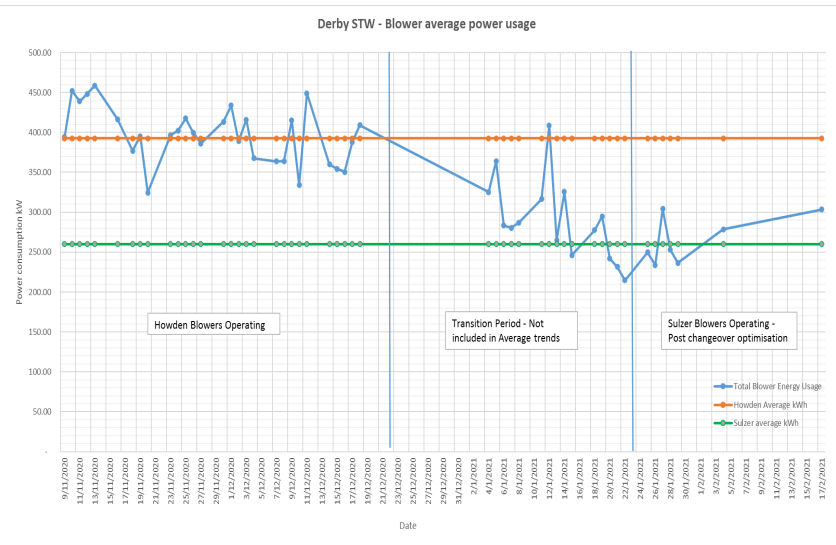
“In water industry energy savings are primary consideration and it this case they allowed the funding of this important project” – explains David Wood. “But there are many other benefits. We now have strategic backup blowers and do not just operate on critical number available. Installing new Sulzer blowers positively impacted the works as the obsoleted blowers would have definitely affected treatment level. Reduced maintenance is obviously a great advantage – no oil or water maintenance required, only air filters and no wearing parts. We value very much reduced noise in Sulzer aircompressors and their compact size gives us more open, spacious environment”.
Following completion of the project, a noise assessment was carried out. Severn Trent’s Health and Safety team were able to confirm that historical noise restrictions could be removed and thus operatives working in the blower house basement no longer need to wear hearing protection.