Business continuity and contingency planning have always played an integral part in the success of any organisation, but with the events of the past couple of years presenting unforeseen (and unprecedented) challenges to those across the water and wastewater industries, preparation has never been more important.
With the ongoing turmoil relating to supply chain disruption, increased cost of materials, and fuel shortages – the results of Brexit, Covid, and more recently the conflict in Ukraine – the reliance on supportability engineering (or Integrated Logistic Support – ILS) and the reassurances it can provide in terms of managing and minimising project risk has increased for many.
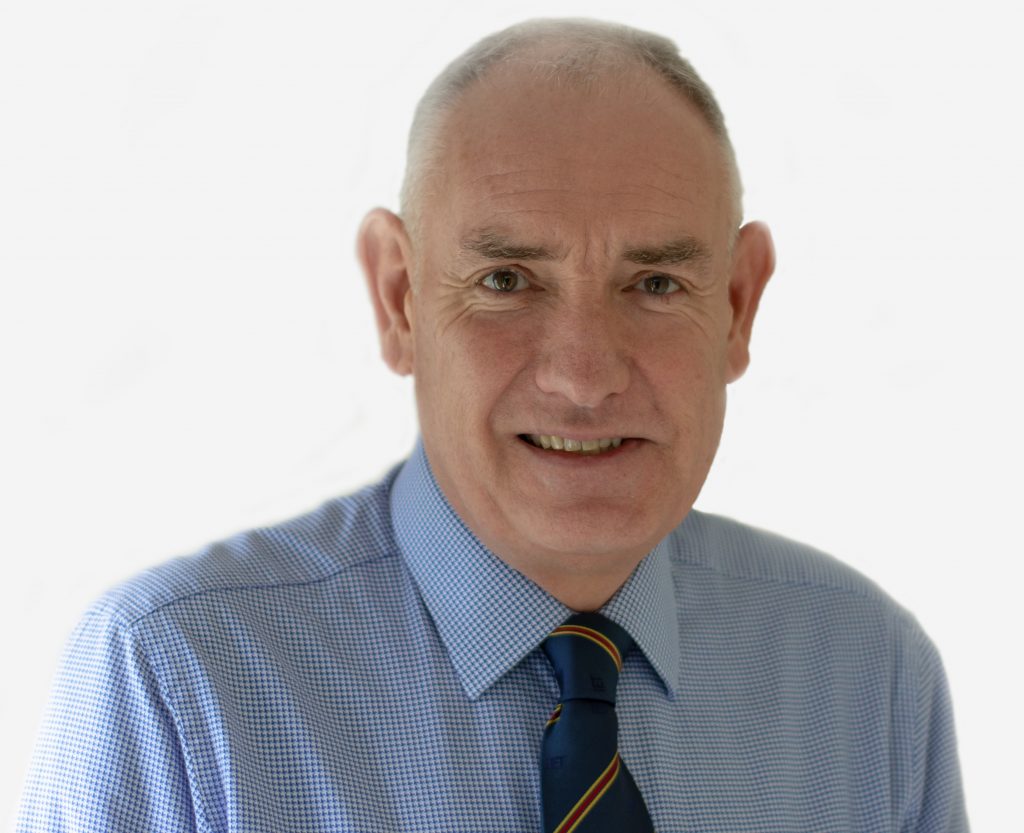
Trevor Hirst, Operations Director at ILS consultancy Quorum, shares an overview of the discipline and its importance in the effective delivery of projects across the industry, the potential implications of getting it wrong (or failing to integrate it effectively), and what the sector should be considering moving forward.
ILS is essentially about ensuring your organisation and all those across your supply chains have the right knowledge and support to be able to deliver a project (physical or virtual) cost-effectively. And, with strains on time, money, and resources ever-increasing, having processes and procedures that minimise risk, avert over-budgeting, meet stringent safety standards, and mitigate project delay are not only hugely valuable, but absolutely project critical.
As a discipline, ILS was first introduced to the UK by the defence sector in the 1950s, and its proven effectiveness as a military tool has attracted the attention of many other sectors – including the water industry – as a means of managing costs, ensuring efficient supply chains, and reducing maintenance costs.
From the development of large-scale sewage treatment works and hydrogen power projects to ongoing pollution control and storm water storage, ILS covers every element in the engineering procurement process – from initial concept design and development through to successful contract and physical engineering, testing, and delivery – plus ongoing maintenance and any servicing requirements.
Essentially, ILS encompasses all areas of through-life management, including:
- Technical Documentation | covering system descriptions, operating information, diagnostic support data, and software information
- Reliability & Maintainability (R&M) | the analysis associated with identifying when a component, sub-system, or system may fail, and what to do about it if it does
- Training Needs Analysis | used to determine all team training requirements and the most effective means of meeting these
- Supply Support Planning | ensures that equipment has a defined supply support structure in place, including spares pipeline, stocking rate, and lead times
- Project Management | ranging from the mentoring and training of existing teams to specialist personnel outsourcing and full external ILS management
- Safety & Environmental Protection | identifies, tracks, and resolves safety and environmental hazards and quantifies and manages risk associated with these
- Human Factors Integration | effectively integrates equipment, systems, and personnel
Through strategic planning and the focused application of ILS, it’s possible to ensure that the designed system is usable, sustainable, and that it fully meets the required capability during its intended lifespan – in the most cost-effective and operationally effective manner. And much like the way Building Information Modelling has been integrated into the build, management, and operation of assets across the water industry, ILS brings together all parties – from OEMs and engineers to operators, logistics, and commercial teams, ensuring they work seamlessly to execute any ILS plan.
The risks associated with not properly integrating or entirely overlooking ILS processes can have a significant impact on organisations, contractors, and of course, those the industry serves. And these risks can include:
- Inaccurate understanding of equipment failure rates | leading to inadequate spare parts holding and subsequent higher risks of increased downtime, lack of productivity, and project delays
- Incorrect calculation of the necessary trained manpower and resources required to successfully deliver (and maintain) a project | leading to potentially lower-quality project outcomes, higher costs, and longer timescales
- Lack of management around the supportability of equipment throughout its required lifetime | leading to equipment becoming unfit for purpose and/or dangerous
- Inconsistent and/or inaccurate documentation | leading to significant risks to safety, as well as inefficiencies and errors
With some of the most common challenges in water and wastewater construction projects relating to document anomalies, sequence of construction, and coordination and communication issues*, the role of ILS is to not only identify potential project risks, but to also outline and provide solutions to mitigate the impact and likelihood of these. Providing assurances to the water and wastewater industry that all and any equipment will not incur additional and unplanned costs throughout its intended lifespan, that it will be delivered within specific timescales, and that the sector and all of its stakeholders benefit from engineering projects that are absolutely fit for purpose.
With the industry leading the way in terms of focusing on performance of an asset rather than simply the asset itself, ILS can play a vital role in further supporting the sector to successfully deliver projects that meet required budgets, timescales, and standards. In addition, helping those across the water and wastewater supply chains to tackle the growing number of challenges, and to support, deliver, and champion best practice for project viability – now and in the future.
*Archis Ambulkar | “Guidance for Professional Development in Drinking Water and Wastewater Industry”